The Importance of Quality Control in Metal Fabrication for OEMs
In metal manufacturing, quality control is critical to ensuring success. Even a single defective part can lead to costly warranty issues, recalls, and possibly catastrophic damage to a company’s reputation and overall brand. That is why Enterprise Welding & Fabricating prioritizes quality and recognizes the important role it has in maintaining reliability and trust.
Precision
Sheet metal fabrication components require an exceptional level of skill, where precision is key — often dealing with materials that vary in thickness, composition and processing. In metal fabrication, even the smallest mistake can compromise an entire project, underscoring the importance of accuracy at every step.
Consistency
Original equipment manufacturers (OEMs) depend on consistent, repeatable results. If you’re making thousands of parts, each item must be precise. This is where our quality team and process controls shine! By performing initial PPAP validation and implementing controls and in process inspection at every step of production, we ensure each component meets the same high standards, batch after batch, year after year, over the past five decades!
It takes time
Quality control is not a one-time task; it’s an ongoing process that begins from the very start and continues throughout. Here’s what that journey looks like:
– Material inspection: It all starts with the materials. Before production begins, we thoroughly inspect every sheet and purchased component required ensure it meets the customer print specification and/or standards.
– Process checks: As parts move through different manufacturing stages, in process controls and inspections are put in place to assure quality and to monitor any variation in the process. This saves time and money down the road during the assembly phase and/or prevents future possible warranty issues.
– Capital equipment and tools: Adopting the latest innovative equipment not only boosts efficiency and throughput but also enhances quality. Modern capital equipment comes with supporting capability studies that demonstrate how innovation leads to greater precision and accuracy. Many of the latest processes feature automation, scanners and camera-based technologies integrated into the equipment, providing an additional layer of quality assurance. As a result, the need for check gauges and manual quality inspections is diminishing, ensuring consistent quality over large quantities and long product life cycles.
– Final inspection: Before any part is shipped to our customers, the item must still undergo a thorough final inspection. This final step is to ensure that it meets all the required specifications and quality standards.
Not only machines do the work
While technology plays a role in modern quality control procedures, the expertise and reliability of employees are equally vital. Advanced tools can enhance accuracy and efficiency, but without skilled technicians and operators who understand the nuances of the process, technology alone cannot guarantee consistent quality. Trained professionals bring the necessary insight, experience and attention to detail that ensure the highest standards are met at every stage of production. Investing in a knowledgeable team, training, coaching, and mentoring is just as important as investing in advanced technology.
Improvement
Quality control isn’t just about meeting minimum standards. It’s about getting better all the time. The team at Enterprise Welding is always looking for ways to improve our processes, reduce variability and push the limits of what is possible in metal fabrication. For example, look at the impact of RF+ on manufacturing efficiency, or how we tackle challenges with our quality scanning technology.
Why it matters for OEMs 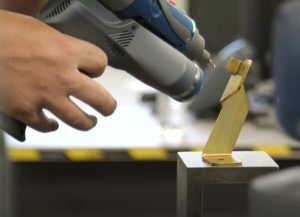
When OEMs choose a metal fabricator that is serious about quality control, it pays off in a lot of ways:
– Lower costs: We catch and fix issues early, helping OEMs avoid expensive rework or recalls later.
– Faster time to market: Consistent quality means fewer hiccups and smoother production runs, allowing OEMs to get their products out faster.
– More substantial reputation: High-quality components lead to high-quality final products, boosting the OEM’s reputation in the market.
– Peace of mind: Knowing that every part meets strict quality standards means OEMs can focus on innovation and growth instead of dealing with quality problems.
Conclusion
Quality control is a mindset that affects all aspects of our work at Enterprise Welding & Fabricating. Our OEM partners rely on us to provide products that are as precise and high quality. We ensure that we consistently surpass those expectations by investing in advanced technology, educating our staff and following quality control procedures.
Quality control is essential in the field of metal fabrication for OEMs. It distinguishes between good and outstanding, between meeting and exceeding expectations. And that is our daily goal that we focus on daily at Enterprise Welding & Fabricating.
“RIGHT THE FIRST TIME & EVERY TIME!” – ENTERPRISE WELDING!